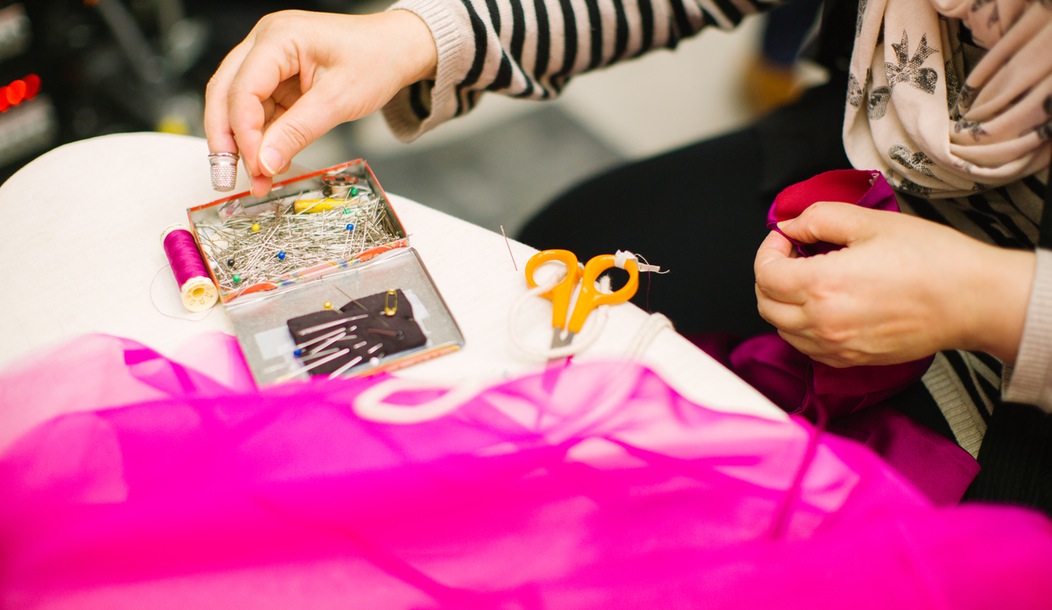
Of all the questions and advice seeking that I receive from new and emerging fashion brands, the topic that is most often addressed is production. From “How do I work with a manufacturer?” to “My samples are horrible! What went wrong?!”, the trials and tribulations are aplenty.
This is because production is one of the most challenging parts of launching a fashion brand. Finding the right factory for your collection and then communicating properly with the people who are making your clothing is not something you can just wing. Planning and preparation are really important.
So when a designer asks me about where to even start in the whole manufacturing process, I always say two things:
- Go through your pre-production checklist.
- Create a tech pack.
Once you know you’re ready to work with a factory, have researched which factories makes sense for your brand, and have started to have a dialogue, Oone thing you need to have ready to present to your factory is your tech pack.
Tech packs are those things we’re all pretty sure we need to give to our factories but aren’t quite sure what they entail.
You don’t want to wing it with this one. The wrong info in your tech pack could mean the wrong finished sample. That means that tech packs are an incredibly important fashion business tool when you’re communicating your designs and specifications to your sample maker and factory.
The more detail you can give them, the less room for mistakes. The clearer you make your requests, the less likely there will be misinterpretations. The more you have in writing, the less likely you’ll be financially responsible for fixes.
Cover Page
The Cover Page houses the basic front and back view of the style. These sketches should have a white or transparent fill, and not contain color or print. The sketches can be computer generated, hand drawn, or photographs. An important concept to be mindful of is to make sure that the image is proportional and clean, meaning they should not be stylized.
Inspiration Page
The Inspiration Page houses any image(s) which helped create the original style. If the factory is to be the source of the pattern, the image(s) may help the factory create the pattern and reach the designer’s desired aesthetic. Inspiration images may contain whole garments or detail pictures, such as close up photos of a pocket or collar. An explanation of why the inspiration image is important may also be needed so the correct aspect of the image is conveyed in the style.
Callouts Page
The Callouts Page is used to articulate the type of construction and design details that should be used when constructing the garment. Be sure to use arrows to clearly mark what type of construction is to be used where. Also be sure that the factory understands any special phrases or acronyms that may be used to abbreviate words.
Print-Fabric Placement Page
The Print-Fabric Placement Page is used to indicate where you would like print and/or fabric. The front and back sketch of the style is colored in relation to a color key at the bottom of the page. This color key makes it very easy to distinguish the desired placement for each type of fabric. Prints could also be used to convey the placement of fabrics; such as one fabric being dots,
and one fabric being stripes. Just make sure to clearly label the key.
Colorway Page
The Colorway Page identifies the colors which are to be used in the design. The current tab format includes several areas to input color information, and grids can be easily copied and pasted to create more information areas. Each color area contains sections for the color name, color number, and color swatch. The color number may be the pantone color number or an original
number. If any other information is needed, simply edit the format so there are more columns in each information area.
This page may also hold print colorways if the design is not going to be one solid color. A true to size print out with color key may also/or instead be needed to identify each color in the print.
Bill of Materials Page
The Bill of Materials Page; also known as the BOM, is comprised of all materials used in constructing the garment. There are five main sections contained in this tab, which are as follows: Fabrics, Trims, Labels, and Packaging.
In each section there are five types of information that can be identified. This information includes Placment (where the material will be used or in what position it will be sewn into the garment), Comments (any extra means that are necessary to understanding the use of the material), Material (the fiber content, identification number, or substance the material is made of), Supplier (the provider of the goods), Color Number ( the item color to be used).
Fold Page
The Fold Page expresses how the garment should be folded and packed. This pack will then be shipped to the desired destination. This page should contain a series of sketches showing the step by step process of folding and packing a shirt. Each sketch has a description for easy directional reference. If sketches cannot be created, a series of step by step photos with explanations would be an acceptable alternative. A description without any supporting images can also be used, however the explanations need to be very clear and easy to follow.
Label Placement Page
The Label Placement Page explains the type of label that is to be used in the product, and where it should be placed. Remember, the material the labels are made of can be found in the BOM.
Proto Specs Page
The Proto Specs Page indicates the measurements to which the pattern and first fit sample should be developed to. The chart contains five columns of information.
- The Point of Measure (POM) indicates how each part of the style needs to be measured to ensure the garment or handbag is the correct size and fits correctly.
- The Description expresses how and what needs to be measured in correlation to the POM code. It should be specific enough to relay what and how the point should be measured. The acronym for ‘high point of shoulder’ (HPS) will be seen often. Most vertical measurements will be measured from HPS, and should be indicated in the description.
- The Requested indicates the actual measurements that the garment or handbag should be developed from. If there is uncertainty of what a measurement should be, the column may be left blank and a note made for the factory to help determine the necessary measurement. The spec can then be measured and filled in at the first fit.
- The Tolerance (+/-) indicates the most a measurement is allowed to be over or under the requested measurement. This number is very important during production, so that the specs of the product are in the approved range of measurements.
- The Comments is for adding important notes.
1st Fit Specs Page
The 1st Fit Specs Page holds all spec information about the first fit sample of development. It includes all five columns of information in the proto specs an adds these additional columns:
- The Actual column is the area in which the measurements of the fit sample are inputted to help visually compare them to what specs were requested.
- The Revised column is the area to input the measurements that the next sample or production should meet.
2nd Fit Specs
The 2nd Fit Specs Page is identical to the 1st fit specs page, except in this page the Requested column is pulled.
1st Fit Comments Page
The 1st Fit Comments Page includes all corrections that need to be made to the 1st fit sample. The fit and construction of the product should be reviewed and commented on. All tabs that took part in the development and creation of the first fit sample should be reviewed as well, to make sure all aspects of the product were followed correctly.
2nd Fit Comments Page
The 2nd Fit Comments Page is exactly the same as the 1st Fit Comments page, noting any errors in fit and construction.
Graded Specs Page
The Graded Specs Page holds the measurements for all sizes that will be put through production.
Anna Taylor
Hey,
Thanks for sharing this resource with us. I found your post by google and it is very informative. I am looking forward to getting a post about the future of fashion tech.
Thank You.
Casey Cline
We’re glad you found this post helpful, Anna!
swathy
Nice blog,
Thanks for sharing this wonderful fashion update.
Fashion Designing Courses in Chennai
Casey Cline
We’re glad you found it helpful!
Javier Hidalgo
Great article Nicole. very nice detailed and helpful.
Eloise
Awesome article! Manufacturing is always the biggest breakdown. You’ve included additional tips here that I don’t use – and I will now!
Thanks Nicole – keep them coming!
X
Nicole Giordano
Awesome! Glad it was helpful, Eloise.